UT Drone
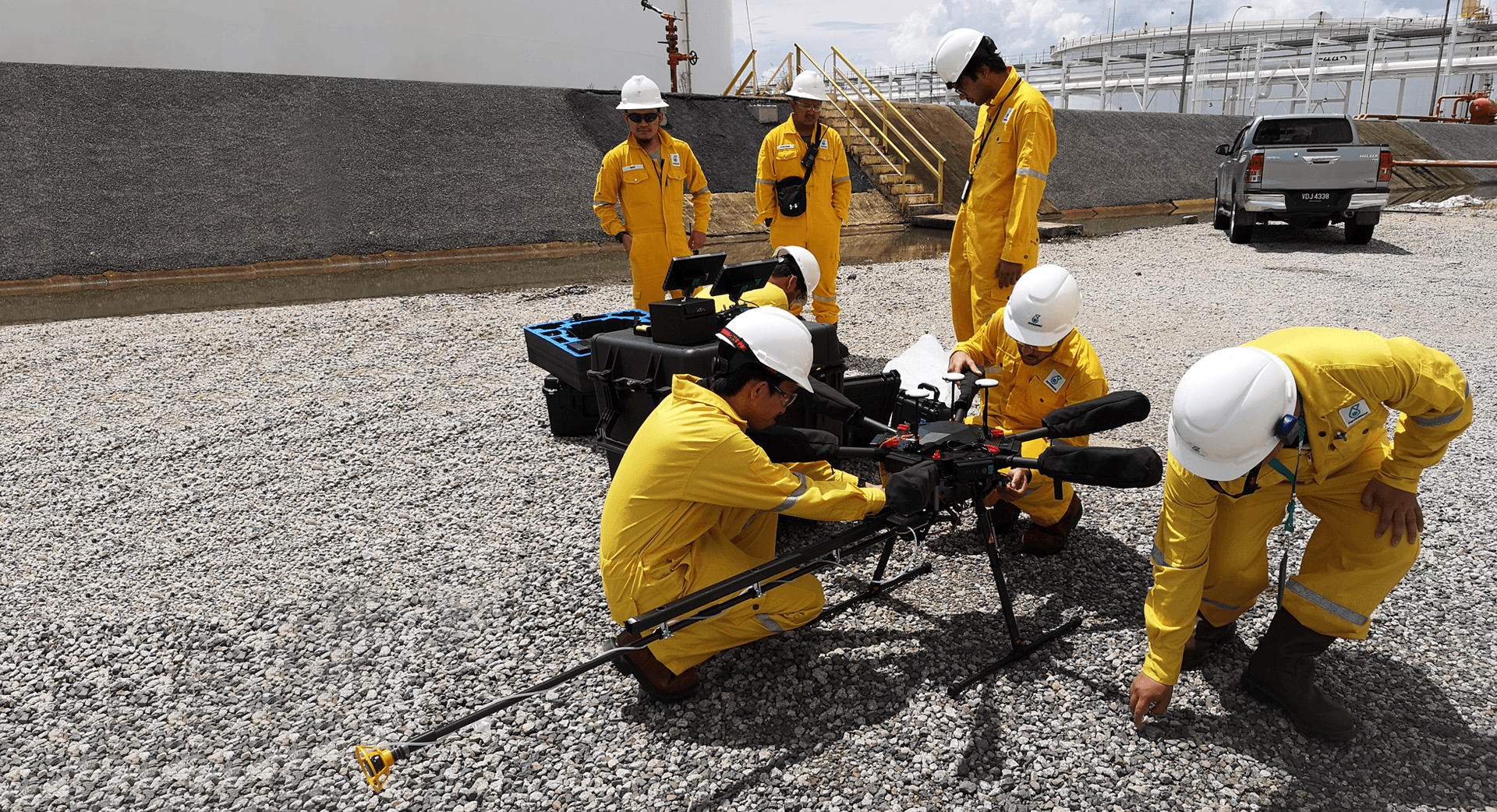
1. Safety Improvement: Reduces HSE hazards by eliminating scaffolding and minimizing confined space entry.2. Efficiency and Cost Savings: Eliminates the need for cranes, scaffolds, and extensive manpower, lowering costs.3. Advanced Technology: Uses LIDAR and 3D Digital Twin Reporting for precise and autonomous inspections.4. Enhanced Data Management: Provides consistent, repeatable results with improved workflow and locational awareness based on 3D modeling.5. High Accuracy: Achieves accurate wall thickness measurements validated against manual inspection results.
Current UT measurement practices at height rely on hand-held probes and scaffolding, leading to high costs, inefficiencies, and significant health, safety, and environmental (HSE) hazards. Inspection of storage tanks and structures typically requires cranes, scaffolds, rope-access, and extensive manpower.
The innovative UT measurement system uses LIDAR and 3D Digital Twin Reporting for autonomous navigation and 3D asset scanning. This system eliminates the need for scaffolding, reduces HSE risks, improves inspection accuracy, and provides consistent, repeatable results with enhanced data management workflows.
This UT measurement system integrates 3D Digital Twin Reporting for better operations, LIDAR for precise autonomous navigation and 3D scanning, and an onboard PC for real-time processing. It minimizes confined space entry and scaffolding use, ensuring safer and more efficient inspections with high accuracy.